FF SERIES - ROTARY NETT WEIGHT FILLERS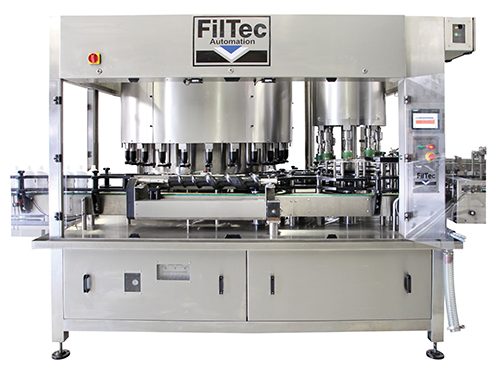
Filtec Automation offers a range of Rotary Nett Weight Fillers, to fill a wide range of products from food and beverage, cosmetics and pharmaceutical applications. Each machine can be configured to handle a variety of products and packaging sizes to ensure maximum flexibility and productivity.
The Nett Weight fillers are offered with options such as, a Foil Capper, “Pick 'n Place” or “On the Fly” capping options utilising Screw Cap, Snap Cap and RO Capping heads, as well as servo controlled capping heads for torque specific applications as well as cap orientation, either vibratory or rotary cap unscramblers with cap elevators. Controls are via touchscreen HMI and can incorporate fully automated height adjustment when changing bottles as well as adjustable CIP operations.
The Nett Weight Filler tares the bottle prior to filling then measures the weight of the bottle as it is filled shutting the nozzle when the desired weight is reached.
The filling principle is extremely simple with an infeed scroll and star wheel moving the containers into the filling area. The containers are lifted on a cam, onto the nozzles, which can be either, 2 stage filling nozzles with a fast and slow filling cycle, or single stage nozzles, which then fill the bottles to the desired volume before transferring to the capping turret and onto the exit conveyor.
The Rotary Capper is available in a number of options including, servo controlled capping turret, conventional screw capping turret with variable torque magnetic clutches and “Snap-Cap” turret, is a Pick 'n Place or on the fly Capper and is supplied complete with cap unscrambler. The machine is supplied complete with one set of change parts. All change overs are very quick and easy as the change over requires no special tools. Change parts are simply replaced and height adjustments are made before production can resume.
Product is generally pumped to the manifold on the filling turret in order to create a pressurised fill, which is fully adjustable from the HMI Touchscreen to suit any application, to minimise the filling time and thus maximise production. The pump is also used during the CIP cycle to ensure that the required fluid velocity is achieved to properly clean all pipework.
Machines are available in both standard configuration for the food and general applications as well as a GMP compliant configuration which maximises cleanability for pharmaceutical applications.